Modern fabrication technologies.
Our USA-based ISO 13485-certified facility is equipped with multiple laser processing stations and cleanrooms to incubate your next medical device project.
-
Laser Welding
Enables high speed, flexible combination, and cleaner fluid channels. Eliminates adhesive residue within fluid channels.
-
Automated Assembly
Enables devices to scale to high volumes and allows for reproducible product performance while eliminating technique dependency.
-
Laser Cutting
Delivers fine line, micron-level feature sizes and enables non-contact, tool-less production.
-
Precision Lamination
Allows for lamination of ultra thin, fine materials and creation of multilayered subassemblies in web format. Enables reduction of touch points on product.
-
Reagent Dispensing
Enables necessary biochemistry to occur inside targeted areas on device.
-
Laser Ablation
Enables direct integration of electrodes into devices. Creates pockets for vents and reagent reservoirs.
-
Molding
Enables integration of blister packs, piercing structures, and deep reagent reservoirs.
-
Laser Drilling
Enables electrical and fluidic interconnections between substrates. Enables breathability of certain areas for controlled out-gassing. Enables fluidic inlet and outlet ports to another device.
-
Coating
Enables desired surface energy characteristics. Enables integration of on-device electrodes.
-
Die Cutting
Enables low cost method of delivering non-Critical to Quality (CtQ) features.
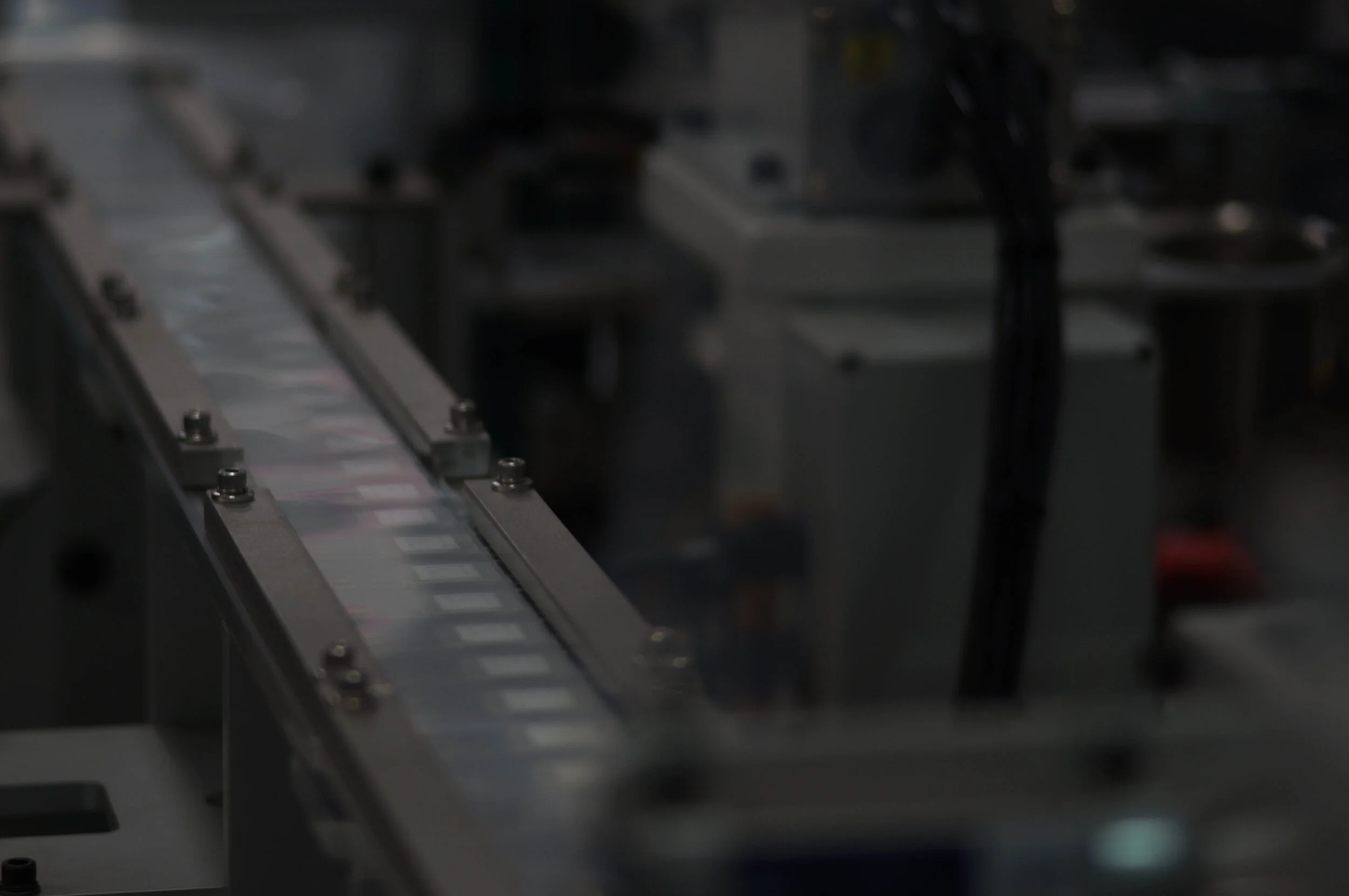