Biochip subsystem technologies.
Our USA-based ISO 13485-certified facility is equipped with multiple laser processing stations and cleanrooms to incubate your next medical device project.
-
Mixing
Leverage any of a variety of passive or active microfluidic mixing approaches.
-
Metering
Leverage thin film wells and layout to accurately meter fluids down to 1uL or less.
-
Gasketing
Leverage thin film elastomer interfaces to manifolds or other mated components.
-
Venting
Leverage various membrane technologies to vent pneumatic and/or fluidic channels.
-
Valving
Leverage thin film elastomer valve technology to open and close pneumatic and/or fluidic channels.
-
Reagent Integration
Leverage on-board reagents via lyophilized beads, functionalized membranes, direct spotting, and/or blister packs.
-
UDI
Leverage laser marked codes, RFID tags, and/or digital printed codes to create unique device identifiers at every level of your device and packaging.
-
Cooling
Leverage thin film heat sinking or transfer technologies to remove heat according to your assay needs.
-
Electrodes
Leverage thin film laser ablated or digitally printed electrodes.
-
Sample Input
Leverage sample input approaches whether it be swab, pipetted liquid, or direct capillary intake.
-
Waste Collection
Leverage thin film wells or injection-molded reservoirs to securely encapsulate your device.
-
3D Fluidic Channel Networks
Register thin film layers +/- 75um and channel sizes ≥100um in thin films ranging from 10-500um in thickness.
-
Heating
Leverage thin film heating technologies to add heat according to your assay needs.
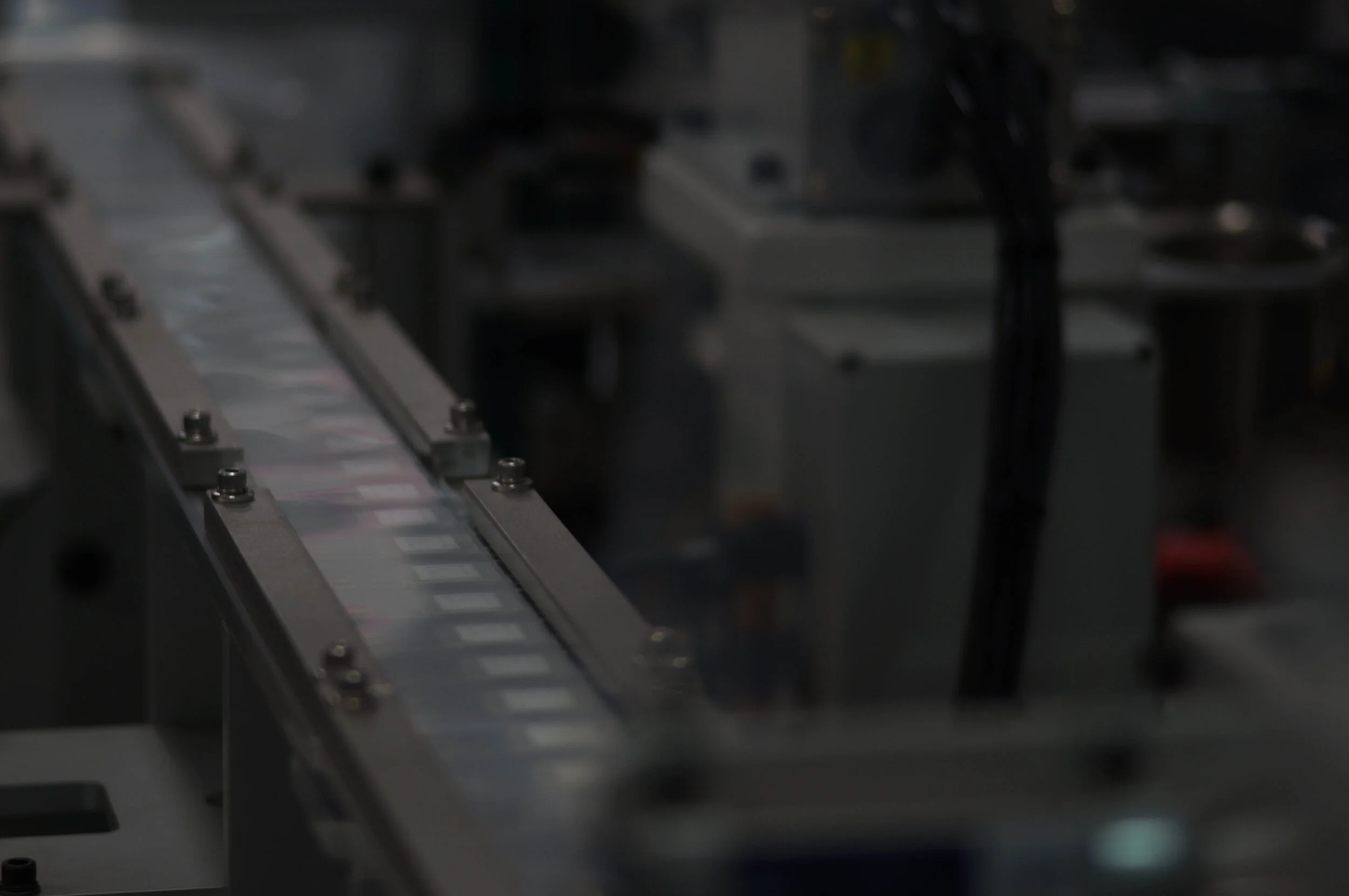